Understanding the Essentials and Applications of Plastic Extrusion in Modern Production
In the world of modern manufacturing, the method of plastic extrusion plays a crucial duty. Untangling the principles of this procedure discloses the true versatility and potential of plastic extrusion.
The Basics of Plastic Extrusion Process
While it may appear complex, the principles of the plastic extrusion procedure are based upon relatively straightforward principles. It is a manufacturing process wherein plastic is melted and then shaped right into a continual account via a die. The raw plastic product, frequently in the kind of pellets, is fed right into an extruder. Inside the extruder, the plastic undergoes heat and pressure, causing it to melt. The liquified plastic is after that compelled with a shaped opening, referred to as a die, to develop a long, continuous product. The extruded product is cooled down and afterwards reduced to the preferred length. The plastic extrusion process is thoroughly utilized in different industries due to its cost-effectiveness, flexibility, and efficiency.
Different Sorts Of Plastic Extrusion Methods
Building upon the standard understanding of the plastic extrusion process, it is needed to discover the different techniques associated with this production method. The two main techniques are profile extrusion and sheet extrusion. In profile extrusion, plastic is melted and created into a continuous account, usually made use of to develop pipes, poles, rails, and home window structures. In comparison, sheet extrusion creates large, flat sheets of plastic, which are normally further refined into items such as food packaging, shower drapes, and car parts. Each technique calls for specialized machinery and specific control over temperature and stress to make certain the plastic keeps its form throughout cooling. Recognizing these methods is essential to making use of plastic extrusion efficiently in modern-day production.
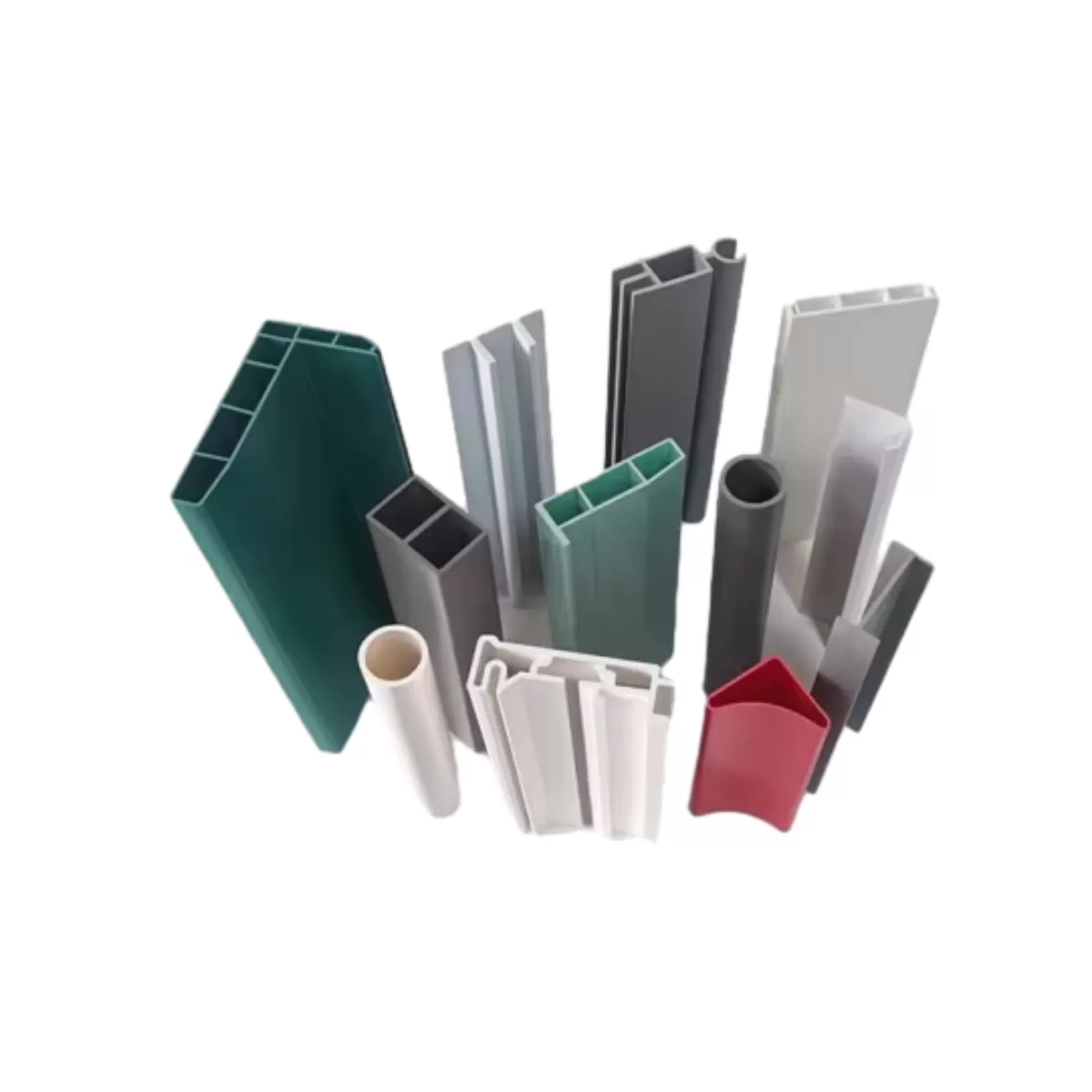
The Duty of Plastic Extrusion in the Automotive Market
A frustrating majority of components in contemporary cars are products of the plastic extrusion procedure. This process has actually revolutionized the automobile sector, changing it into an extra effective, economical, and versatile production field. Plastic extrusion is largely used in the production of different auto components such as bumpers, grills, door panels, and dashboard trim. The process provides an uniform, regular outcome, making it possible for makers to generate high-volume get rid of excellent precision and very little waste. The lightness of the extruded plastic parts adds to the general reduction in car weight, boosting fuel effectiveness. The durability and resistance of these components to warmth, cold, and effect boost the longevity of vehicles. Hence, plastic extrusion plays an essential role in vehicle production.
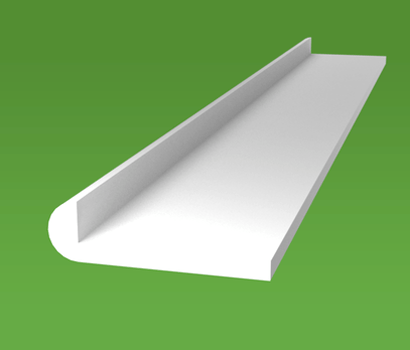
Applications of Plastic Extrusion in Durable Goods Production
Past its considerable influence on the auto industry, plastic extrusion verifies similarly effective in the world of customer items making. The flexibility of plastic extrusion allows suppliers to make and generate complicated forms and sizes with high precision and effectiveness. The adaptability, flexibility, and cost-effectiveness of plastic extrusion make it a preferred selection for many customer products suppliers, contributing dramatically to the market's development and technology.
Ecological Impact and Sustainability in Plastic Extrusion
The pervasive usage of plastic extrusion in manufacturing invites scrutiny of its eco-friendly effects. As a process that frequently utilizes non-biodegradable products, the ecological impact can be considerable. Energy consumption, waste manufacturing, and carbon exhausts are all concerns. Market improvements are raising sustainability. Reliable machinery minimizes energy use, while waste monitoring systems reuse scrap plastic, reducing basic material i was reading this needs. Additionally, the growth of naturally degradable plastics uses a more eco pleasant option. In spite of these enhancements, additionally advancement is required to alleviate the ecological impact of plastic extrusion. As culture leans in the direction of sustainability, producers must adapt to continue to be feasible, stressing the importance of continuous research study and advancement in this area.
Final thought
Finally, plastic extrusion plays an essential function in modern manufacturing, specifically in the vehicle and customer goods markets. Its flexibility permits the manufacturing of a large range of elements with high accuracy. Additionally, its potential for reusing and growth of naturally degradable products offers a promising method towards lasting practices, thereby resolving environmental concerns. Comprehending the essentials of this procedure is crucial to maximizing its advantages Your Domain Name and applications.

The plastic extrusion process is thoroughly used in different industries due to its flexibility, cost-effectiveness, and performance.
Structure upon the basic understanding of the plastic extrusion procedure, it is essential to explore the various methods entailed in this manufacturing technique. plastic extrusion. In comparison, sheet extrusion creates large, level sheets of plastic, which are usually more processed into items such as food product packaging, shower curtains, and automobile components.An overwhelming majority of parts in contemporary automobiles are items of the plastic extrusion procedure
Comments on “Plastic extrusion for pipes, sections, and custom shapes”